Developing a Welding WPS: Step-by-Step Directions for Professionals
Developing a Welding WPS: Step-by-Step Directions for Professionals
Blog Article
Achieving Welding Excellence: Introducing the Keys of WPS Execution and Optimization
In the realm of welding, attaining quality is a pursuit that pivots on the meticulous execution and optimization of Welding Procedure Requirements (WPS) By delving into the essential elements, methods, obstacles, and finest practices connected with WPS, a world of welding excellence awaits those that are prepared to explore its midsts.
Importance of WPS in Welding
The Relevance of Welding Procedure Specifications (WPS) in the welding sector can not be overstated, acting as the foundation for making sure consistency, quality, and safety and security in welding procedures. A WPS provides thorough instructions on just how welding is to be performed, consisting of crucial variables such as materials, welding procedures, joint design, filler steels, preheat and interpass temperature levels, welding currents, voltages, traveling rates, and extra. By adhering to a well-defined WPS, welders can preserve harmony in their work, bring about consistent weld top quality across various projects.
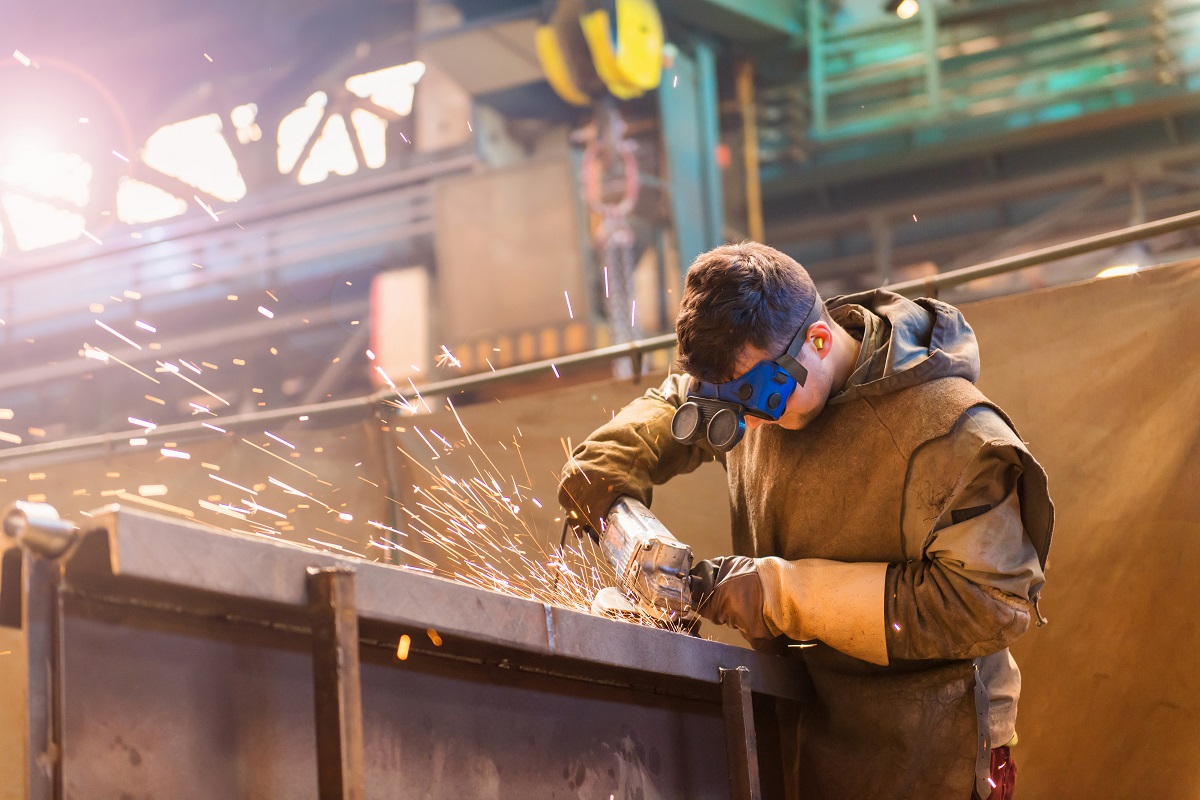
Secret Aspects of WPS
Discussing the indispensable parts of a welding treatment spec (WPS) is essential for understanding its duty in welding operations. A detailed WPS includes numerous crucial elements that lead welders in accomplishing quality and consistency in their job. One critical facet of a WPS is the welding process requirements, which outlines the certain welding procedures to be used, such as gas tungsten arc welding (GTAW) or shielded steel arc welding (SMAW) Furthermore, the WPS consists of details on the welding materials, such as the kind and specifications of the base metal and filler steel to be used. The WPS additionally specifies necessary variables like welding criteria, preheat and interpass temperature level requirements, and post-weld warm treatment procedures. Moreover, it includes details on joint design, fit-up, and any type of unique methods or preventative measures necessary for the welding procedure. By integrating these crucial elements right into the WPS, welding treatments can be standardized, ensuring top quality, efficiency, and security in welding procedures.
Methods for WPS Optimization
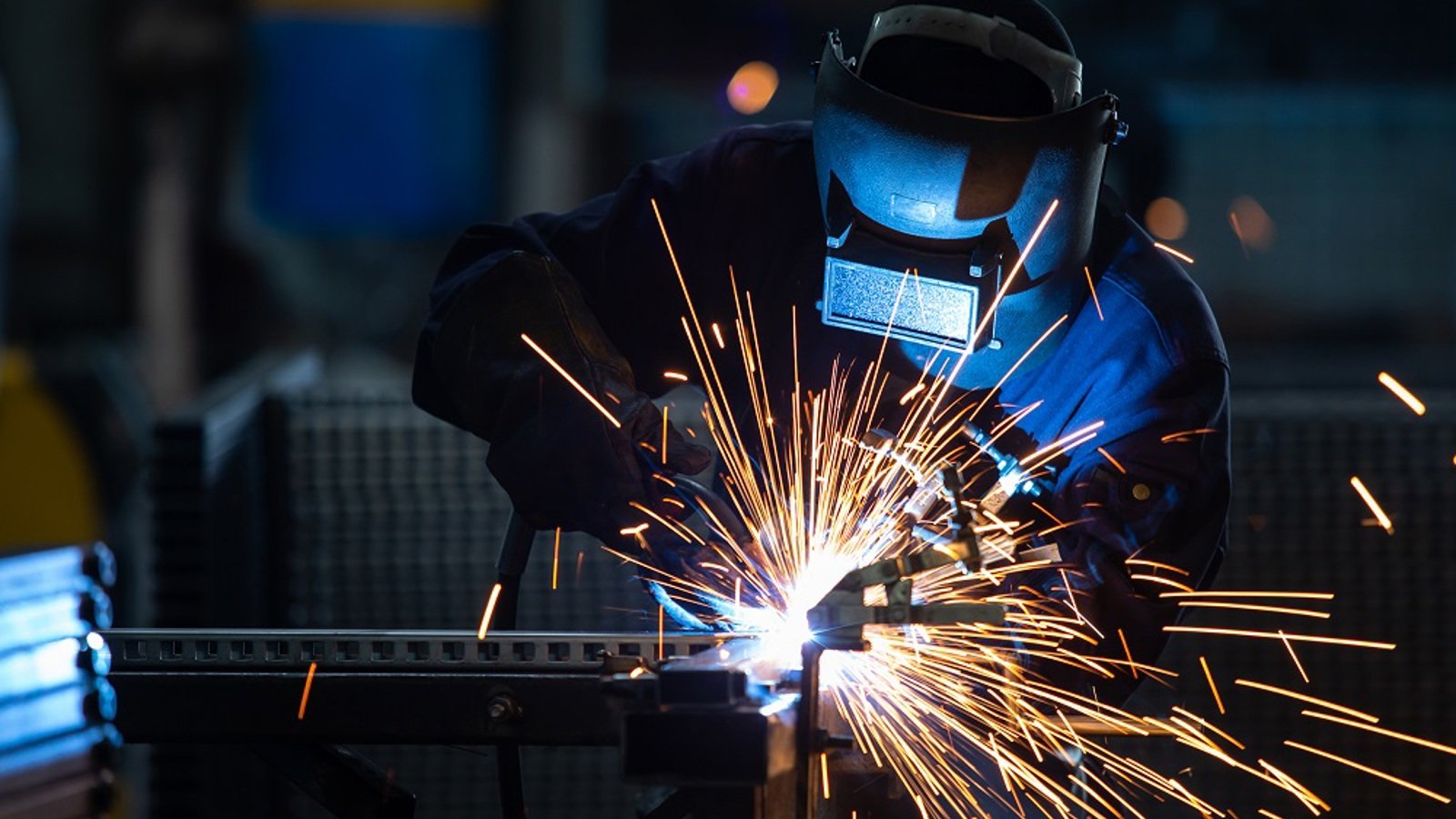
Second of all, training and qualification of welding employees according to the particular needs of the WPS is paramount. Giving comprehensive training programs and ensuring that welders are certified to execute treatments described in the WPS can bring about higher top quality welds and decreased rework.
In addition, leveraging modern technology such as welding software and monitoring systems can aid in maximizing WPS. These tools can help in tracking variables, ensuring specifications are within defined limitations, and providing real-time comments to welders, allowing them to make prompt adjustments for improved weld high quality.
Usual Difficulties and Solutions
Dealing with challenges in applying the strategies for WPS optimization can prevent welding procedures' performance and high quality. One usual obstacle is insufficient training or understanding of the welding procedure specifications (WPS) amongst the welding group.
One more challenge is the absence of correct documentation and record-keeping, which is necessary for WPS optimization. Without clear records of welding parameters, materials made use of, and evaluation results, it ends up being difficult to determine locations for enhancement and ensure uniformity in welding processes. Carrying out a robust paperwork system, such as electronic welding management software program, can assist streamline record-keeping and promote data evaluation for continual renovation.
Additionally, irregular welding equipment calibration and upkeep can position a significant challenge to WPS optimization. Normal equipment checks, calibration, and upkeep schedules need to be abided by purely to guarantee that welding criteria are precisely regulated and preserved within the defined tolerances (welding WPS). By resolving these typical obstacles with positive services, welding procedures can enhance effectiveness, top quality, and general welding quality
Finest Practices for WPS Implementation
To make sure effective WPS application in welding procedures, adherence to industry standards and careful focus to detail are vital. When launching WPS implementation, it is important to begin by extensively understanding the particular welding demands of the task. This requires an extensive evaluation of the welding treatment requirements, products to be bonded, and the ecological problems in which the welding will certainly happen.
When the demands are clear, the following action is to select the ideal welding procedure that lines up with these specs. This includes getting in touch with the appropriate codes and requirements, such as those like it given by the American Welding Culture (AWS) or the International Company for Standardization (ISO), to make certain conformity and top quality.
Additionally, documenting the entire WPS application process is vital for traceability and quality assurance. Thorough documents should be kept relating to welding specifications, material preparation, preheat and interpass temperatures, welding consumables made use of, and any kind of discrepancies from the original procedure. Regular audits and testimonials of the WPS can aid recognize areas for improvement and ensure recurring optimization of the welding procedure.


Final Thought
Finally, the application and optimization of Welding Treatment Specifications (WPS) is important for achieving welding excellence. By recognizing the crucial elements of WPS, carrying out reliable methods for optimization, addressing typical obstacles, and following best methods, welders can make certain top quality welds and risk-free working problems. It is necessary for experts in the welding market to prioritize the appropriate execution of WPS to boost overall welding performance and attain wanted end results.
The Importance of Welding Procedure Specifications (WPS) in the welding industry can not be overstated, serving as the backbone for ensuring consistency, quality, and security in welding operations. A WPS offers in-depth directions on exactly how welding is to be brought out, including essential variables such as materials, welding processes, joint design, filler metals, interpass and preheat temperature levels, welding currents, voltages, travel speeds, and a lot more. One vital aspect of a WPS is the welding procedure requirements, which lays out the details welding procedures to be utilized, such as gas tungsten arc welding (GTAW) or protected metal arc visit their website welding (SMAW) By try this web-site incorporating these vital components right into the WPS, welding procedures can be standardized, ensuring quality, performance, and safety and security in welding procedures.
It is important for experts in the welding sector to focus on the proper execution of WPS to enhance overall welding performance and achieve wanted end results.
Report this page